Наконец-то собрался и написал пост про то, как я работал на заводе.
Примечание: так как мои бывшие коллеги точно не захотели захотели бы публиковать свои фотографии в интернете, я заменил все лица портретом Франца Кафки (который заодно символизирует всю безысходность завода).
Мои первым серьезным местом работы (до этого были, по сути, экскурсии в работу) стал завод под названием СП «Фребор». Ему я посвятил два с половиной года своей жизни. И именно благодаря ему я понял, что голову нужно использовать не только для ношения шапки. Уже прошло пару лет, как я не работаю на «Фреборе», однако этот завод иногда мне снится. Наверное, таким образом он просит меня написать про него небольшую статейку. Что ж, завод, уговорил, пишу.
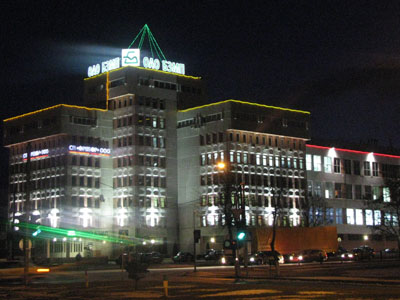
Нарядный новогодний завод. В центральной “башенке” (где зеленая пирамида) находилась наша раздевалка. А сам цех располагается примерно в полукилометре от раздевалки.
Итак, СП «Фребор» (полное название «Фрезениус Диализотехник Борисов») – это совместное белорусского-германское предприятие по производству медицинской техники: капельниц, катетеров, диализаторов и прочего. В начале девяностых годов хитрые немцы пришли к выводу, что очень выгодно открыть свой заводик в какой-нибудь нищей восточноевропейской стране: рабочая сила там дешевая и экологические стандарты не такие строгие. В качестве такой страны была выбрана Беларусь. Свои цеха «Фребор» разместил на территории другого медицинского предприятия – «Борисовского Завода Медицинских Препаратов».
Цех, куда я устроился на работу в августе 2009-ого года, производил полисульфоновое волокно. Это волокно вставлялось в диализаторы, которые необходимы для очистки крови (интересующиеся могут погуглить по словосочетанию «диализ крови»). Насколько я знаю, подобное производство является единственным в Беларуси. «На волокнах» работают аппаратчики формования химволокна: четыре бригады по 12-14 человек каждая. Работают в три смены по скользящему графику (по четыре дневных, вечерних и ночных смены). Чтобы получить почетное звание аппаратчика, необходимо сперва четыре месяца поработать учеником. А учиться там было чему. Итак, постараюсь рассказать все по порядку.
Есть прядильная линия (у нас их было две, но это не так важно) – громоздкий металлический агрегат длиной около пятидесяти метров и высотой около трех. В начале линии есть специальные блоки, на которые под давлением подается предварительно приготовленный раствор из полисульфона и растворителя. Из блоков выходит множество тонких нитей, которые попадают в осадительную ванну с горячей водой. Нити твердеют, а затем оказываются в промывочных ваннах, где (как понятно из названия) они промываются. После промывки нити оказываются в сушильных камерах (я думаю, вы догадаетесь, что там происходит). После этого этапа нити уже становятся полноценным полисульфоновым волокном. И тут вступают в игру аппаратчики.
Чтобы вам было понятнее, чем занимаются аппаратчики, рекомендую посмотреть вот это видео (снято на телефон Nokia E63, в центре кадра – я).
Если после просмотра стало еще не все понятно (или у вас ограничен траффик и потому видео – непозволительная роскошь), то расскажу кратко принцип работы. Волокно, которое мотается на барабаны, поступает непосредственно из последней сушильной камеры. Когда барабан совершит нужное количество оборотов, его следует сменить на пустой. Барабан с волокном переносится на стол, где происходит формование пучка. Каждый сегмент барабана оплетается специальной пленкой и скотчем, а затем пучки по одному отрезаются.
Пучки оказываются на конвейере, который ведет на участок упаковки. Упаковщиками становились по очереди все члены бригады. Задача упаковщика – визуально проверить качество пучка и положить его в коробку. После наполнения коробка запечатывалась и отправлялась в путешествие в другие страны (либо на второй этаж, где собирали диализаторы для использования в Республике Беларусь).
Итак, почему на аппаратчика формования химволокна нужно учиться четыре месяца?
1) Нужно научиться лепить нормальные пучки: без складок, гармошки из скотча, неровностей и прочего. Со стороны кажется, что делать это достаточно просто. Однако когда становишься за барабан, отрываешь кусочек скотча и берешь в руку пленку, то ощущаешь себе паралитиком, который пытается восстановить моторику рук. Первое время кажется, что никогда не сможешь даже просто «лепить пучки». Не говоря уже о том, чтобы делать это так быстро, как твои коллеги. (Для справки – полный барабан пучков нужно слепить и порезать примерно за минуту-полторы, чтобы успеть снять другой, уже намотанный барабан).
2) Резать пучки тоже надо учиться, но в сравнении с лепкой это сущие пустяки.
3) Научиться ставить барабан на наматывающее устройство. В принципе, в сравнении со следующим пунктом, это не так сложно:
- Ставишь барабан на наматывающее устройство;
- Достаешь «хвост» волокна из инжектора, просовываешь его в спицу барабана и завязываешь вокруг специального крепления.
4) Научиться снимать барабан. Вот это для меня было очень сложно. Для того, чтобы снять барабан, нужно было:
- Взять ножницы вот таким хватом, как на фотографии;
- Включить инжектор, куда заводится хвост волокна;
- Левой рукой приподнять волокно, захватить его правой рукой таким образом, чтобы оно проходило через лезвия ножниц и указательный и средний пальцы.
- Быстро сжать руку в кулак, чтобы разрезать волокно. При этом один конец волокна должен быть зажат в правой руке, второй – заведен в инжектор.
- Махнуть ногой около фотоэлемента на полу, чтобы отключился магнитный замок барабана;
- Снять барабан и отнести его на стол.
Все эти операции нужно было выполнять быстро и аккуратно. А съём и постановку барабана – очень быстро и очень аккуратно. Ведь в случае ошибки волокно начнет путаться и наматываться на многочисленные валы и гребенки. Особенность производства полисульфонового волокна такова, что нельзя сказать «горшочек, не вари» (волокно идет непрерывно, 24 часа в сутки). Невозможно остановить линию на пять минут, распутать узел на одном валу и снова запустить линию. Потому все исправления проводились «на живую», то есть в процессе генерации волокна. В случае каких-либо запутываний приходилось обрывать волокно до места «косяка», чтобы один человек мог вручную тянуть его («тянуть кишку»), а остальные в это время обрывали намотавшиеся на валы нити, чтобы вернуть работоспособность прядильной линии.
Особенно круто было, когда обрыв случался в одной из сушильных камер. Рабочая температура там около 100-130 градусов. При открытии камеры она несколько падала, но все равно приятного было мало. А в эту камеру надо было лезть, чтобы распутать волокно. Велик был риск получить ожог, если по неосторожности коснешься плечом какой-нибудь горячей металлической детали внутри камеры.
Раз в год прядильные линии останавливались на пару дней для масштабного профилактического обслуживания. Несколько раз в год – для мелкого ремонта. Также регулярно происходили обрывы. Во всех этих случаях было необходимо заправлять линию, чтобы возобновить производство.
Если не ошибаюсь, обычно заправка линии занимала около восьми часов, то есть стандартную смену. Этот процесс требовал большого умения и сноровки. Заправкой линии занимались наиболее опытные аппаратчики («отцы», как они называли сами себя, или «старые зонтики», как называли их мы, более молодые аппаратчики). Не буду подробно описывать процесс заправки линии да не помню его уже толком. Проведу лишь аналогию. Представьте, что у вас есть пучок из множества нитей, который с достаточно большой скоростью без остановки отматывается от катушки. Вам нужно провести эти нити через несколько сотен валов и гребенок, при этом ни на одном из них нити не должны запутаться. Адски монотонная, нудная и очень ответственная работенка – всего одно неосторожное движение могло похерить работу одного-двух часов.
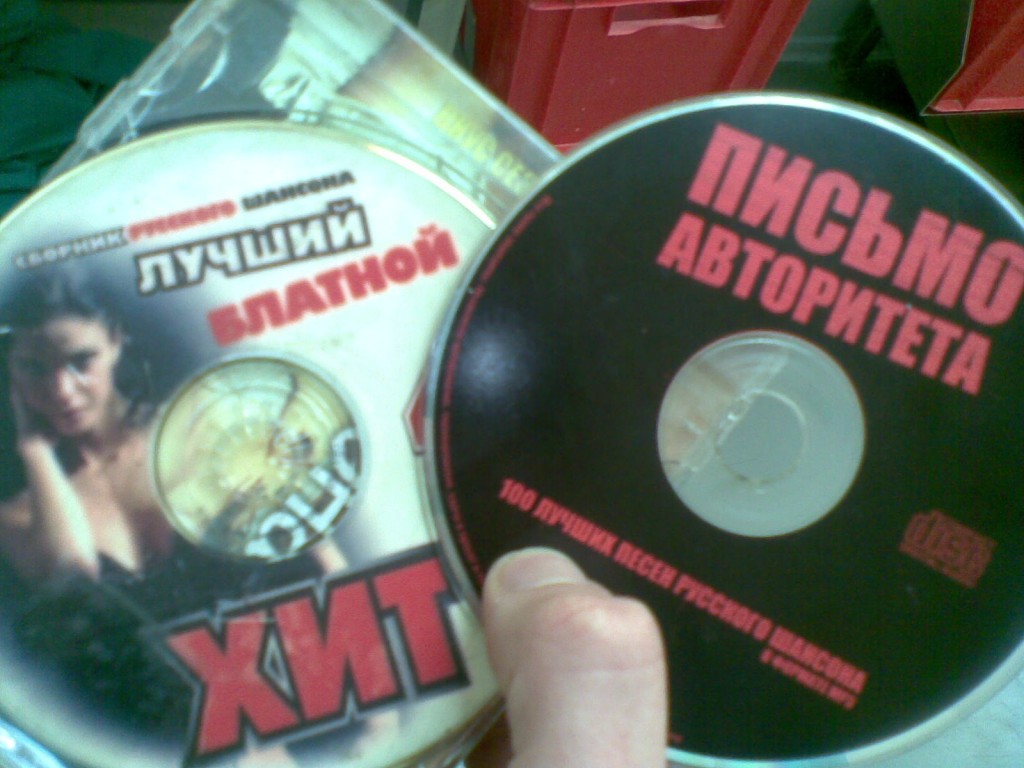
Чтобы разнообразить тяжелую заводскую жизнь, мы слушали в цеху бодрящий русский шансон.
Как я уже говорил, производство волокна идет безостановочно. Потому для обеспечения работоспособности линии было сформировано четыре бригады, которые ходили на работу посменно, по скользящему графику: три бригады разбивали сутки на три смены по восемь часов, а четвертая в это время отдыхала. Следовательно, выходными для аппаратчиков были не субботы, воскресенья и государственные праздники, а свои собственные выходные, которые определялись графиком. Потому Новые 2011-ый и 2012-ый годы я встретил в буквальном смысле на работе. Но именно за все эти тяжелые и неудобные условия я благодарен заводу. Если бы там работалось гораздо проще, то я бы не набрался смелости и не ушел бы оттуда, а остался бы там, регулярно бухая и ненавидя себя.
Вроде бы кратко описал все аспекты работы. Если кому-то что-то интересно или непонятно – спрашивайте в комментариях. При необходимости дополню этот материал отсутствующей информацией.
И напоследок небольшой медитативный коуб
Да уж скрыл лица,не поспоришь))
и твое тоже)
и моё))))
и все же красиво ты лепил))
Лепил как бог))))